Equipment Change Makes Operations & People More Safe and Efficient
Lincoln Industries in Nebraska is the nation’s largest privately held metal finishing company. They were looking for a smart way to upgrade the efficiency of their warehouse operations. Lincoln Industries uses lift trucks for nearly all of their material handling needs.
They were relying on an aging fleet of 26 lift trucks to move product through the 334,000 sq. ft. facility. They knew the process could be improved and wanted their unique culture to be important aspect of the upgrade.
The company is very people-oriented and wanted to ensure productivity, collaboration and safety were all a priority throughout the process . They have been named one of the Top 25 Best Medium-Sized Companies to Work for in America on five occasions.
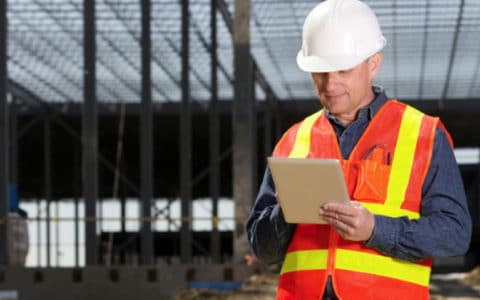
INITIAL CHALLENGE
Lincoln Industries wanted their fleet of lift trucks to perform more efficiently and safely. The trucks were more than five years old so the fleet was in need of some updates.
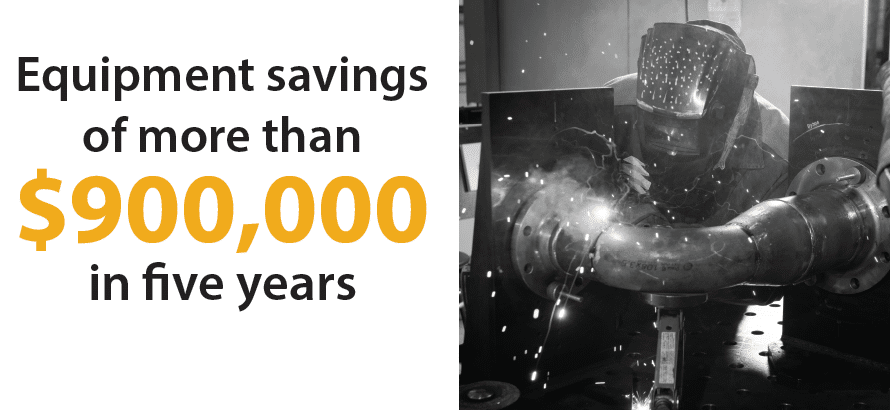
OUR SOLUTION
Riekes worked with Lincoln Industries to complete an in-depth facility assessment. Riekes identified a $180,000 annual savings by implementing side-shifting forklift attachments and iforks which also helped improve the efficiency and safety of the plant.
THE RESULTS
The truck operators saw immediate improvement in productivity. With the implementation of new battery and fleet management systems, Lincoln Industries was able to free up warehouse space for more production. They also saw an increase in level of safety by adding laser attachments and side-shifting fork postitioners which allowed for fork adjustment from the truck without having to exit the vehicle. The fleet was implemented in February and Lincoln Industries broke sales records in 4 of the next 6 months.